
Using the fish-bone diagram is fundamentally against the engineering-based convergent thinking that would ask first the major fundamental questions (e.g.

The first company to adopt the diagram in all. The tools or rather methods they contain are used for defect recording and failure analysis. Ishikawa diagram is a tool for visualizing the cause-and-effect relationships of a specific situation or problem in order to detect the root cause. The "Measurement" cause category also should not be in the fish-bone, as we should already know in the D2 (Problem description) whether we have a measurement system error, or a real product problem. The Fishbone Diagram was originally created by Kaoru Ishikawa to find process imperfections (Ishakawa, 1985).Understand the technical root cause(s) first, and only then go deeper to managerial ones (with 5 x why).

The "Management" cause category should not even be in the fish-bone, as it is not technical. The fishbone diagram is a powerful process improvement technique which greatly helps to determine the important factors involved in a process.
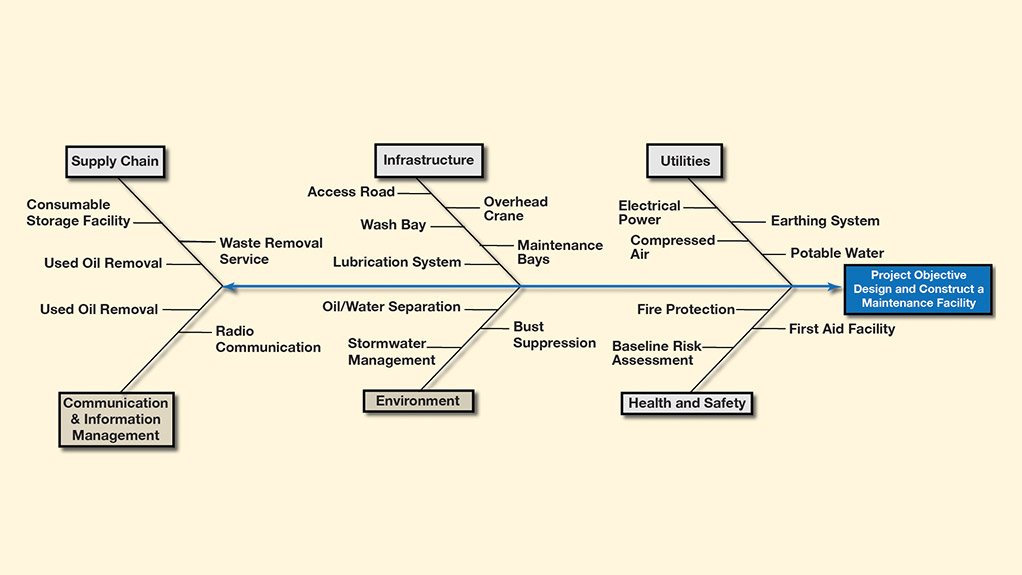
Big iskikawa = you did not understand your fundamental problem, and your technical "storyline". The fishbone diagram (or Ishikawa diagram) helps managers identify the root cause of any problems, defects, or failures.First documented by Kaoru Ishikawa in the 1960s, it is used to this day as a cornerstone. Enforces brainstorming instead of structured convergent thinking. An Ishikawa diagram is a graphical method for root cause analysis. The Cause and Effect Diagram (Fishbone Diagram) from Japanese quality control statistician Kaoru Ishikawa is a graphical technique that can be used in teams.
